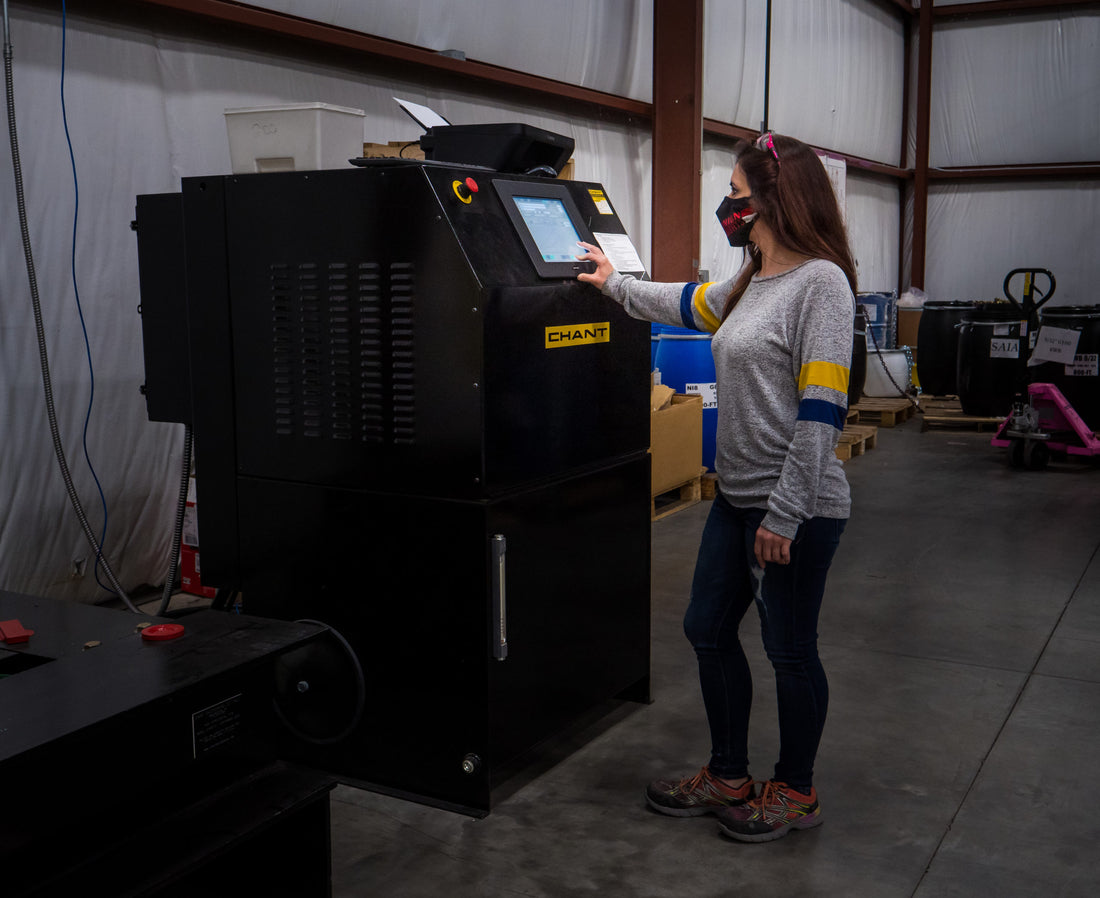
Key Factors to Having a Test Bed, and What This Means for You
US Cargo Control just got a brand new toy in the house, and it's a horizontal test bed! For the past few months, we've been experimenting with this equipment that will help us run more efficiently and grow as a company, create time and cost-saving solutions, and provide customers what they want, when they need it.
What is the Purpose Behind the Test Bed?
Also known as a proof test machine, the test bed has several different purposes that meet all of our needs. It can help us add new and potential capabilities, ensure our current product verifications are being met, and give us confidence we're giving customers products that have been successfully tested for quality and accuracy.
The most important reason we have our own test bed in-house is it'll make sure that the products we're supplying meet the needed Working Load Limits (WLL) and Break Strengths (BS). If you'd like to learn more about the WLL and BS, read what the numbers on your load-bearing equipment mean.
This machine serves our mission to get the customer the quality products that they deserve. We sat down with one of our experts, Wendi Kafer, to learn the key factors to having this machine.
What is the Test Bed?

It is a horizontal test bed from Chant Engineering which has the capacity to conduct tension or proof test up to 150K LB on our lifting slings and tiedown straps. The products are placed in the testbed and pulled to their WLL or beyond, depending on what pull test you are wanting to conduct.
Although its intended use is for the lifting industry, we can also test load-bearing equipment for the trucking and moving industries.
Why Did US Cargo Control Get a Test Bed?
We initially purchased the test bed to determine the design and verification of our current products and new capabilities. Not only that, it creates better time and cost-saving solutions, which is a win in our books.
If we test our nylon and recovery straps through our 3rd party lab, the costs would have been around $68,000. Because we have our own testing equipment, we can create our own products in-house and this avoids creating continous huge costs.
What Results Have We Seen?

The test bed has given us the ability to test and determine the design and verification for most of our recovery and nylon straps to achieve the results we seek. Along with that, we'll be able to make new and current capabilities in-house instead of drop shipping them!
We also conducted testing on our tiedowns to confirm their tack strengths. For example, we changed the tack pattern on our 3" and 4" tiedowns to significantly reduce the time it takes to produce an assembly. We tested the new tack pattern (according to the WSTDA standards) on our test bed, and we saved 30 seconds per fixed ends and loose ends while still maintaining their strength ratings!
Lastly, we've been able to confirm the Working Load Limit and Break Strength on our custom tiedown straps. As we continue to test our tiedowns with hardware like shackles and chains, we will also work to find the safest and most cost-efficient way to test our full assemblies.
What Does the Test Bed Mean for Our Customers?
Currently, this machine will give us the opportunity to conduct proof load testing that a customer may request on a lifting sling. A proof load test is a type of test that proves the fitness and working load limit of the lifting equipment that it's designed to withstand. This will ensure the lifting equipment works correctly and safely through its operational cycle.
What Products Are We Using Currently with the Test Bed?

We are currently test recovery straps, lifting slings, tiedowns with loops, and potentially some tiedowns with hardware.
Tiedowns with hardware require special hookups to the pins of the machine in order to be pulled. We have the possibility to use shackles, round slings, chains, and more that we have in-house. The straps with hardware will need to be reviewed and be determined if we can currently test at this time.
What's the Process of Testing the Products on the Machine?

The most critical and first step we take is safety. We alert everyone in the area that we will be testing the products and ear protection is available. We place the product in the test bed before closing it, and plug in information in the machine's computer such as the type of test being conducted and the desired Break Strength we would like the product to be pulled to.
After the setup is complete, we will start testing. We can determine if the product fails or passes the test when it reaches the WLL and BS. If it fails, we examine why it has failed and collect the data so we can improve our products for the next test.
We upload the test into our database to file and record on our master testing sheet. We use this data to make improvements if the product fails and if a customer would like the information of the product that passed the testing for their records.
Getting You What You Want, When You Need It
Having the test bed in-house creates excitement at US Cargo Control because we'll be able to confirm verifications ourselves before sending any new products to our website or shipping them to our customers. We enjoy finding new opportunities to continue growing our business, and with our new machine, we'll be able to identify new possibilities so we can continue to be your source for equipment for hauling, rigging, moving, towing, and lifting all kinds of cargo.
We're all ecstatic about this brand new machine and can’t wait to get your orders out of the door and into your hands!